Корпоративные новости
08.12.2021
Ограниченный график работы в период рождественских и новогодних праздников 2021/2022 года
ИНФОРМАЦИЯ ОБ ОГРАНИЧЕННОМ ГРАФИКЕ РАБОТЫ
24.03.2021
Окончание технической и сервисной поддержки систем управления МЭФИ
Окончание технической и сервисной поддержки систем управления МЭФИ
статья для журнала Manufacturing Journal 06 / 2015
26.06.2015
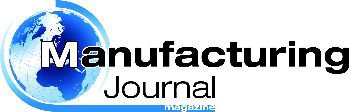
Metallurgical Plant “ELECTROSTAL”
Leading manufacturer of high-quality steel in Russia
Throughout its history Metallurgical Plant Electrostal is a leading manufacturer of high-quali-ty steels. The plant is a major producer of heat-resistant nickel alloys in wide ranges of brandand size - from wire to large-sized forgings. It has the unique metallurgical equipment, providing a complete production cycle of any batches. The plant has more than 2,000 grades of steel and alloys in its range. Experience and quali cation of company specialists greatly accelerate the new product introduction process.
The company with nearly
a century of history
During the First World War Nikolay Vtorov, the wealthiest Russian businessman and industrialist nicknamed “Russian Morgan” for his business acumen, founded several factories for the production of shells and the first Russian high quality alloyed steels making plant. The
first steel was melted by the Plant Electrostal, located 50 km from Moscow, on November 17, 1917. Talking about the rich, nearly a century history of the company, first of all we want to emphasize tradition, experience and technological level of the staf , – says CEO Evgeny Shilnikov. The whole history of the plant is inextricably linked with the “first time” concept. For the f rst time in the country
metallurgists of Electrostal mastered the production of stainless, magnet and ball bearing steel for mechanical engineering and chemical industries; superalloys for jet aircraft and spacecraft; thermostatic bimetals and alloys with special physical properties for instrument making, radio and communications equipment. For the f rst time employees of Electrostal implemented ref ning remelting on an industrial scale, as well as vacuum metallurgy techniques and advanced technological processes of metal deformation, allowing to obtain metal with high quality characteristics. Throughout its history Metallurgical Plant Electrostal is a leading manufacturer of high-quality steel in Russia.
Main products and production
Electrostal of ers its customers more than 2000 steel and alloy grades and impressive range of sizes - from wire to large-sized forgings. Gathered experience and skills of specialists of the Plant allow to promptly put into production new products. Almost all steels and alloys manufactured by Russian metallurgical plants have been developed byspecialists of Metallurgical Plant Electrostal JSC in close cooperation with the leading scientifi-research institutes of the country. The company has uniquely equipped metallurgical facilities such as open arc and induction furnaces, an out-of-furnace steel treatment unit, vacuum induction, vacuum arc, electro slag and electron beam furnaces as well as rolling, press forging and hardware equipment allowing to manufacture any production lot size, from wagon deliveries to several kilograms. Traditional production of the plant includes forged, washers, rods, wire, sheet and strip. Electrostal is one of the main and unique Russian suppliers of starting stock for blades, disks, shafts and rings for gas turbine engines. Currently, the plant started the production of new products of deep redistribution - shafts of variable cross section, discs, rings - with full mechanical and thermal treatment. Thanks to the quality control at all stages of the production process, we can fulfil themost demanding requirements of our
customers. The quality management system and products manufactured by the company are certifid in accordance with international standards, – says CEO.
Strategic potential
The modernization and technical reequipment program, currently implemented at the Plant, allows to signifiantly expand its technical and
manufacturing capabilities, including export potential, and provide a comprehensive supply of high-tech products of top quality. Compny’s key customers include main Russian aerospace companies, defense enterprises, power and oil and gas complexes, auto manufacturers,
engineering and instrument-making plants. Electrostal supplies 10% of its products to the countries of Western Europe. The company has always been a reliable business partner for its customers. Electrostal is a great example of effctive team work (the number ofemployees - more than 5000 people), aimed at increasing the capacity and development of the plant as a whole. The company sees its mission as keeping leadership in the Russian Federation and winning over the European market in production of special and highquality steel. Electrostal consistently implements strategic goals, increasing the level of sales, customer satisfaction and effiency, as well as raising the level of staf competence and motivation. The company is focused on continuous improvement of product quality and application of new technologies to ensure effient production of the required quality at all stages of production. For this purpose the company constantly
conducts marketing researches, making decisions based on data analysis and taking up measures to avoid recurrence of inconsistencies and product defects. The goals and objectives set by the Plant are of the utmost importance, extremely ambitious and unprecedented
at this stage of industry development. However, implementation of such expanded modernization program will ensure stability of the Plant at the market and its long-term development.
New investments and further development plans
The new realities bring new goals and objectives. To maintain a leading position among the enterprises of the domestic steel industry Electrostal contributes to the special program for modernization of the enterprise and its technical re-equipment, providing the
modernization process of special metallurgy, replacement of outdated equipment, energy sector modernization, environmental protection and working conditions improvement. The project is implemented within the framework of scientifi and technical cooperation with
the Russian Federation State Research Center VIAM, based on the signed Scientifi and technical cooperation in the fild of special metallurgy. The Plant and VIAM had also signed a number of licensing agreements for the production of special alloys. The technical reequipment of the enterprise is now in full swing. The plant is on the stage of introduction of modern technological processes in steel works, in the shops of strain redistribution, in units of control and product testing. Modern facilities embodying the most recent advances
in science and technology are supplied by leading foreign companies. Modern equipment provides maximum process automation and minimizes the impact of the human factor. The greatestamount of work was performed on the construction of a deep redistribution of
special steels and alloys complex. The complex includes a 200-MH die-forging press manufactured by Siempelkamp (Germany), two ring-rolling mills by SMS MEER and Siempelkamp and expanders by SMS MEER and Fontijne Grotnes Group (Netherlands & USA). All these
components work in conjunction with specialized manipulators supplied by GLAMA Maschinenbau GmbH (Germany), which is able to provide a wide range of technical capabilities of manipulators and at the same time to take into account all the individual, specifi and
unique requirements of the customers. On the site of the machining processing of forgings and rings there are lathes, delivered in collaboration with the engineering company FINVAL produced by HONOR SEIKI CO. (Taiwan), automated bands by KASTO Maschinenbau GmbH (Germany) and CNC waterjet cutting machine by PTV spol. s.r.o. (Czech Republic). An automated heat treatment line, which contains electric chamber furnaces, quenching tanks with water and oil, the installation of forced air cooling and charging machine was put into operation. This line was designed, manufactured and installed by Electrotherm Electrical & Metal Products Ltd. (Israel), one of the leading companies in the development, design, production and sales of heating equipment including industrial furnaces, heaters, controls
and automation. The band was delivered by GLAMA Maschinenbau GmbH (Germany). At the same time equipment complex for non-destructive testing was put into operation. The complex includes automated line penetrant for product testing by ATG s.r.o. (Czech Republic) and several automated systems delivered by worldwide known company ScanMaster (Israel), for immersion ultrasonic control rods, discs and rings made of special alloys. In the nearest future Electrostal is planning to launch a toolroom, which will meet the needs of primary production and provide it with equipment and tools. Tools Division will be able to fully meet all the needs of the plant in auxiliary equipment, minimize the cost of the fial product, and most importantly, signifiantly reduce the time of the production. The fist batch of a new production of the plant - rings, discs and shafts of variable cross section have been already delivered to a number of plants and now in the stage of scale tests and quality assessment. The Quality Management System of Electrostal certifid for the compliance with
the requirements of AS / EN 9100C and ISO9100: 2008 ensures high quality of developments and products. The Plant has greatly expanded its technical and technological capabilities, and thus the range of products. The modernization program will ensure the plant stable operation and development in the years ahead. There is no doubt that the JSC Metallurgical Plant Electrostal will continue to increase its production capacity and expand the scale of the presence of both domestic and international markets of high quality steel.
Manufacturing Journal 06 / 2015 - скачать